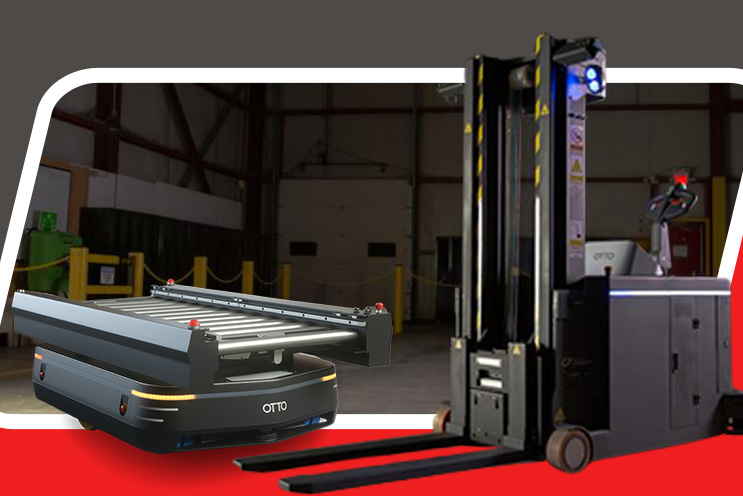
Today, tasks like moving, packing, loading and unloading goods are more advanced than ever. Industries can use state-of-the-art mechanisms to complete operations more efficiently, resulting in fewer labor-intensive tasks and increased productivity and revenue. Improving your processes with robotic automation allows you to stay ahead of your industry, streamline processes, maximize efficiency and enhance working environments.
What Is an AGV?
An automated guided vehicle (AGV) is a computerized vehicle used for tasks like transporting, loading, offloading and retrieving materials from shelves, often in an industrial facility. AGVs follow a programmed route and can complete repetitive tasks like putting items on a pallet. These vehicles are self-operating and use devices like magnetic tape and wires to navigate a warehouse.
What Is an AMR?
An autonomous mobile robot (AGV) is a self-operating robot used for transporting and packing goods and managing inventory, often in a warehouse. This robot uses technological innovations like sensors, algorithms and built-in maps to navigate a facility while automating and speeding up laborious tasks.
AMRs vs. AGVs: Key Differences
Did you know that the AGV market is projected to reach $4.09 billion by 2029, while the AMR market is anticipated to grow by $2.3 billion between 2023 and 2028? One of the main reasons for this growth is these vehicles’ ability to automate processes and enhance efficiency in numerous settings. While these tools share this advantage, they have key differences that set them apart, making them unique for various industries and processes:
1. Navigation
AGVs have lasers, beacons, wires, magnetic tapes and tracks for navigating a predetermined route. These components guide AGVs, helping them detect obstructions and complete tasks. Still, even though AGVs can identify obstructions, like equipment and fallen goods, they have less advanced technology, have determined routes and must follow a predefined path. Additionally, AGVs need human intervention to change routes and navigate around obstacles.
AMRs have more innovative technology for navigating numerous routes than AGVs. With built-in maps, sensors and cameras, AMRs can move freely or travel areas without human intervention. If there is an obstacle, an AMR will independently reroute and “rescue itself,” finding a more efficient path to complete a task.
2. Safety
AVGs and AMRs offer unique safety features. AGVs stop when they detect an obstruction, preventing collisions and other accidents. Similarly, AMRs move out of the way and find an alternative route when they see an obstacle, limiting safety hazards and maximizing efficiency. While AMRs and AGVs are safe to use in various facilities, managers must decide on suitable safety features depending on their applications and safety standards.
3. Installation
AGVs have complex installation processes due to their limited adaptation to new environments. Businesses must consider layout and reconstruction or moving facility infrastructure when installing AGVs. This process can be time-consuming and costly and impact production.
AMRs can integrate seamlessly into existing facilities and infrastructures. There’s no need to change layouts, and businesses can install AMRs in numerous facilities without delaying or stopping operations. Moreover, an AMR system can deployed and tested in a matter of days or weeks, while an AGV system will take weeks to months to process.
Another installation factor to consider is the cost of deployment. Deploying an AMR system is much more affordable, and a dealer can train the customer to adjust the AMR’s operating area. An AGV has to stick to its path — when the customer wants to change the path, the installer must update the system. Ultimately, the AMR is a more flexible and easy-to-deploy technology.
4. Flexibility
Adapting AGVs for different applications can be challenging. Because AGVs operate on a predefined path, changing or altering an application or task can often require modifying hardware and software to support new operations. Buildings can have limitations like insufficient space, preventing AGV alterations.
For example, changing an AGV task can require rerouting wires or moving facility equipment. Rerouting wires can be costly and time-consuming. Additionally, moving equipment might not be possible. For these reasons, AGVs might suit environments with little changes and fixed tasks.
In comparison, AMRs can adapt to new applications and technologies more easily with technology like sensors. Operators can adjust AMRs for different operations with little effort or cost. AMRs are an excellent solution for ever-changing and dynamic work environments with multiple functions.
5. Collaboration
AMRs and AGVS can come in similar sizes, making them versatile for small and large fleets. Additionally, these vehicles can collaborate in varying settings to perform transportation tasks.
6. Autonomy
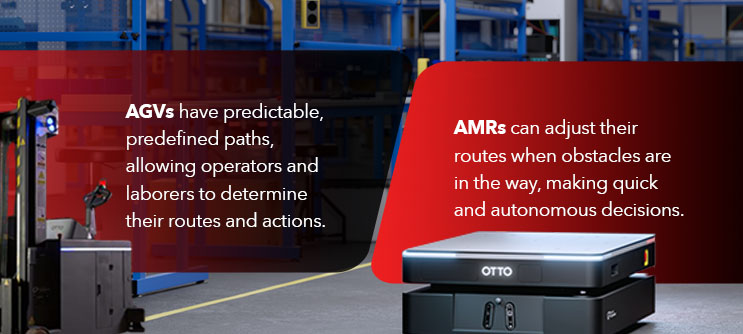
AGVs have predictable, predefined paths, allowing operators and laborers to determine their routes and actions. At the same time, AMRs can adjust their routes when obstacles are in the way, making quick and autonomous decisions.
7. Applications
AMRs and AGVs can support multiple applications. Manufacturers can use AGVs for applications like transporting raw materials in various industries like paper, agriculture and logistics. These vehicles can do laborious tasks, freeing teams for more specialized work. While these robots can accomplish tedious duties more efficiently and dynamically, AMRs have a more advanced system design, enhancing operations.
8. Intelligence
AGVs and AMRs can collect data to enhance future operations, while some AMRs have software that assists in optimizing navigation.
9. Costs
AMRs and AGVs can be priced similarly, and the most significant cost differences come down to deployment and installation.
Infrastructure alterations and renovations to support different AGV operations are considerable cost factors. AMRs have built-in technology and don’t require infrastructure like wires, magnets and tracks, making them more cost-effective to install and deploy.
While AMRs might have more expansive and costly technology, the ease of interaction and the limited need for infrastructure can save you time and money in the long term.
Warehouse Automation
AGVs and AMRs have distinct features for automating and enhancing warehouse operations and can suit different industries and applications in multiple ways.
The Role of AGVs in Warehouse Automation
Manufacturers can use AGVs as substitutes for conveyor systems, forklifts and manual carts to transport heavy goods and materials. AGVs have an onboard platform for storing goods and can feature rollers for lifting materials to platforms without manual labor.
These vehicles can also include additions like a forklift and pallet jack to move and lift pallets. They also offer dual drive and can drive independently or with a human operator.
It’s important to note that while AGVs have some advantages, AMRs have newer technology, can move autonomously and have more capabilities.
The Role of AMRs in Warehouse Automation
AMRs’ new software and technology are leading and transforming the future of the material handling industry. They have multiple attachments for lifting, grabbing and transporting goods and materials. In warehouses, walking and manually moving pallets can be time-consuming, impacting efficiency and productivity.
AMRs can alleviate lengthy processes like transporting merchandise. AMRs can also transport goods to packing areas, reducing the need for employees to walk to and from aisles and packing areas.
AGVs are often the more expensive option regarding total project costs, but once deployed, both AMRs and AGVs can reduce labor-intensive work, improving efficiency. They both improve efficiency. Robots can travel faster to shelves and pick items more efficiently than laborers walking to shelves and sorting through goods. They can also reduce the amount of walking workers do, enhancing their work environment and job satisfaction.
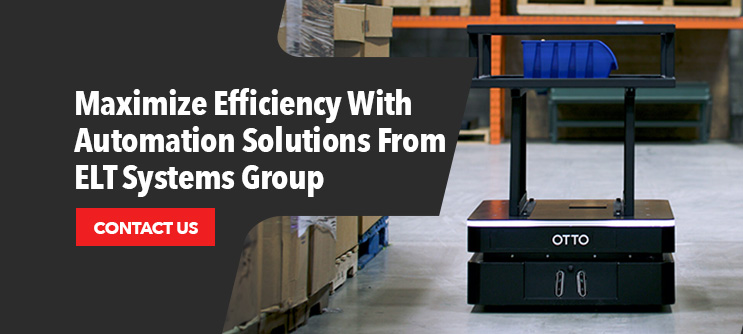
Maximize Efficiency With Automation Solutions From ELT Systems Group
With over 50 years of industry experience, we know the importance of staying competitive and efficient amidst ever-evolving warehouse and factory applications and operations. That’s why we provide innovative robotics solutions like autonomous lift trucks, pallet jacks and forklifts to improve your material handling operations and efficiency.
We partner with reputable brands like OTTO Motors to provide high-quality and reliable integrations. Our solutions are versatile and adaptable to your industry and applications, so we can meet your needs with the right technology. Contact us today to learn more about our robotic automation solutions.