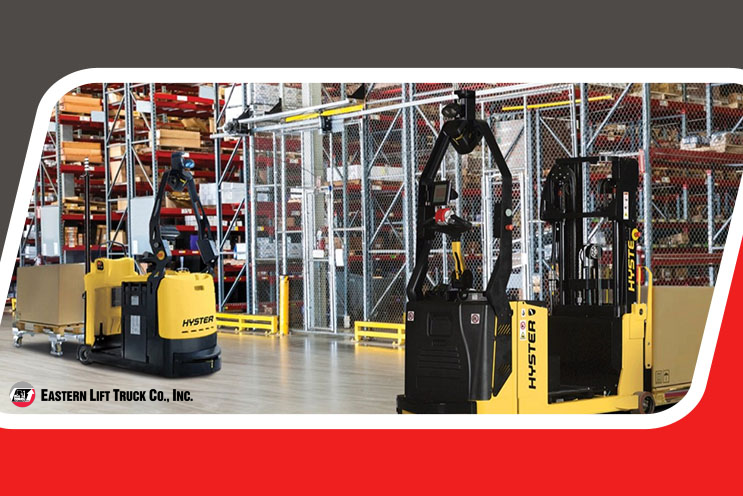
Warehouse automation has transformed the nature of the industry, bringing robotics, equipment and software to nearly every task in the facility. As automation technology becomes more attainable and affordable, warehouse organizations must have a pulse on it. Adopting automation techniques will be crucial to staying competitive and getting ahead of the curve.
As a trusted expert in automation, ELT Systems Group and its knowledgeable engineers have been implementing this equipment for years. We’re well-versed in finding the best solutions for unique businesses, so we’ve compiled a guide to automation options and how they can help your warehouse operations excel.
Types of Warehouse Automation
You’ll find automation used in almost every part of the warehouse, including picking, sorting, returns, receiving, packaging and shipping. Some systems work alongside humans and complement them, while others completely automate tasks, allowing workers to focus on more complex duties. Automation tactics generally work best for repetitive, tedious operations, like picking and sorting, and for tasks that could create safety risks for humans.
With sophisticated and versatile technologies, automation can help warehouses meet an array of diverse goals with affordable entry costs.
- Goods-to-person (GTP): Goods-to-person automation is one of the oldest types of automation, which involves simply bringing materials to the workers. For example, a conveyor belt can transport items around a facility to different areas, like shipping and packing. It can also move them along an assembly line. GTP technology can include cranes and automated vehicles.
- Automated storage and retrieval solutions (AS/RS): AS/RS is a type of GTP automation that uses vehicles, carousels and vertical lift systems to place items in storage and retrieve them. Other types of AS/RS machinery include tote shuttles and mini loaders.
- Pick-to-light systems: Pick-to-light systems, also called put-to-light systems, use LED lights and barcodes placed on racks and shelves to help workers find items. They can significantly reduce walk time for human employees and help them work faster by quickly identifying the correct location.
- Automatic guided vehicles (AGVs): AGVs also move around a facility and transport items. They rely on various sensors, such as magnetic strips, lasers, wires and cameras, to guide them through a defined path in the warehouse. They need a decent amount of space, so AGVs are best used in simple warehouse designs without much human traffic.
- Autonomous mobile robots (AMRs): AMRs are similar to AGVs but much smarter. They use advanced tools like laser guidance systems and GPS to create their routes in real time. They can better accommodate nearby humans and changing environments. For example, we often use AMRs from OTTO Motors. OTTO automation vehicles support scalable and customizable automated lifting tasks.
- Voice picking and voice tasking: Voice picking and voice tasks add hands-free guidance for placement and picking. A worker might use a wireless headset to dictate the item needed, and the system would help create an optimized path and direct them to the best location. These methods can eliminate the need for handheld devices like radio-frequency scanners.
- Collaborative mobile robots: Collaborative robots, also called cobots, work alongside humans to improve productivity. They typically take over menial, repetitive tasks and are designed for safety with lightweight designs and rounded edges.
- Software solutions: Many software systems can help bring automation to warehousing. A warehouse management system, for example, might automate various tasks like re-ordering items or predicting demand.
The Benefits of Automation in Warehousing
While numerous industries depend on automation, warehousing has particularly promising applications. Almost every warehouse can benefit from some level of automation thanks to advantages like the following:
1. Improved Productivity and Speed
Robots and programs can accomplish many of the same tasks as humans with much greater speed, but they also play supporting roles and help human workers finish their tasks faster and more effectively. You can increase throughput and completion times to meet customer demands better and stay ahead of the competition. Automation can also streamline time-consuming processes and minimize waste, allowing you to make the most of your resources.
2. Better Accuracy
Manual processes are prone to error, in part due to the nature of human behavior. Automated processes are typically far more accurate, helping to reduce error rates and costly fixes. They can avoid mistakes in the first place and better identify them for remediation.
3. Worker Safety and Satisfaction
Warehouse environments introduce a wide range of hazards, including many of the most common workplace injuries, such as:
- Falls, slips and trips
- Overexertion
- Exposure to harmful substances or environments
- Contact with objects and equipment
Automated solutions can improve safety by eliminating many of these hazards. For example, robots can carry heavy items, preventing workers from doing so and potentially being injured as a result.
Automated systems also offer the advantage of keeping humans from needing to perform tedious, repetitive tasks, making their workdays more enjoyable and allowing them to use cognitive or creative skills. More satisfied employees can help boost workplace morale and retention rates.
4. Cost Savings
Virtually every warehouse can benefit from the cost savings of automation equipment. A significant advantage comes from the reduction in labor costs. Along with a salary, employees require training, benefits, safety equipment and other resources that take up your budget. Automation systems can reduce the number of workers needed on the floor, allowing you to save on these extensive costs.
Automation can also help you improve your bottom line with more labor availability. In many situations, robotic equipment can run 24/7, delivering the profitability of more uptime. Even if your industry experiences a labor shortage, robots can offer some insulation from these effects.
Although you will need to make an initial investment to get these benefits, today’s automation solutions have a much lower cost of entry than their predecessors. Implementation is more affordable, so you can get a higher return on investment and start using these tools faster.
Start Automating With ELT Systems Group
Automation has revolutionized the warehousing industry, and today’s businesses must keep pace. However, implementing automated systems can be complex. That’s why ELT Systems Group offers comprehensive automation solutions, including project management, design, consultation and sales, to help you find the right mix of equipment and strategy for your facility.
Our experienced application engineers will look at your needs from all angles and help you reap the benefits of automation. Whether your goals involve speed, accuracy, safety or another one of automation’s capabilities, we can help you make it a reality. Contact us today to learn more about automation and see how we can help.