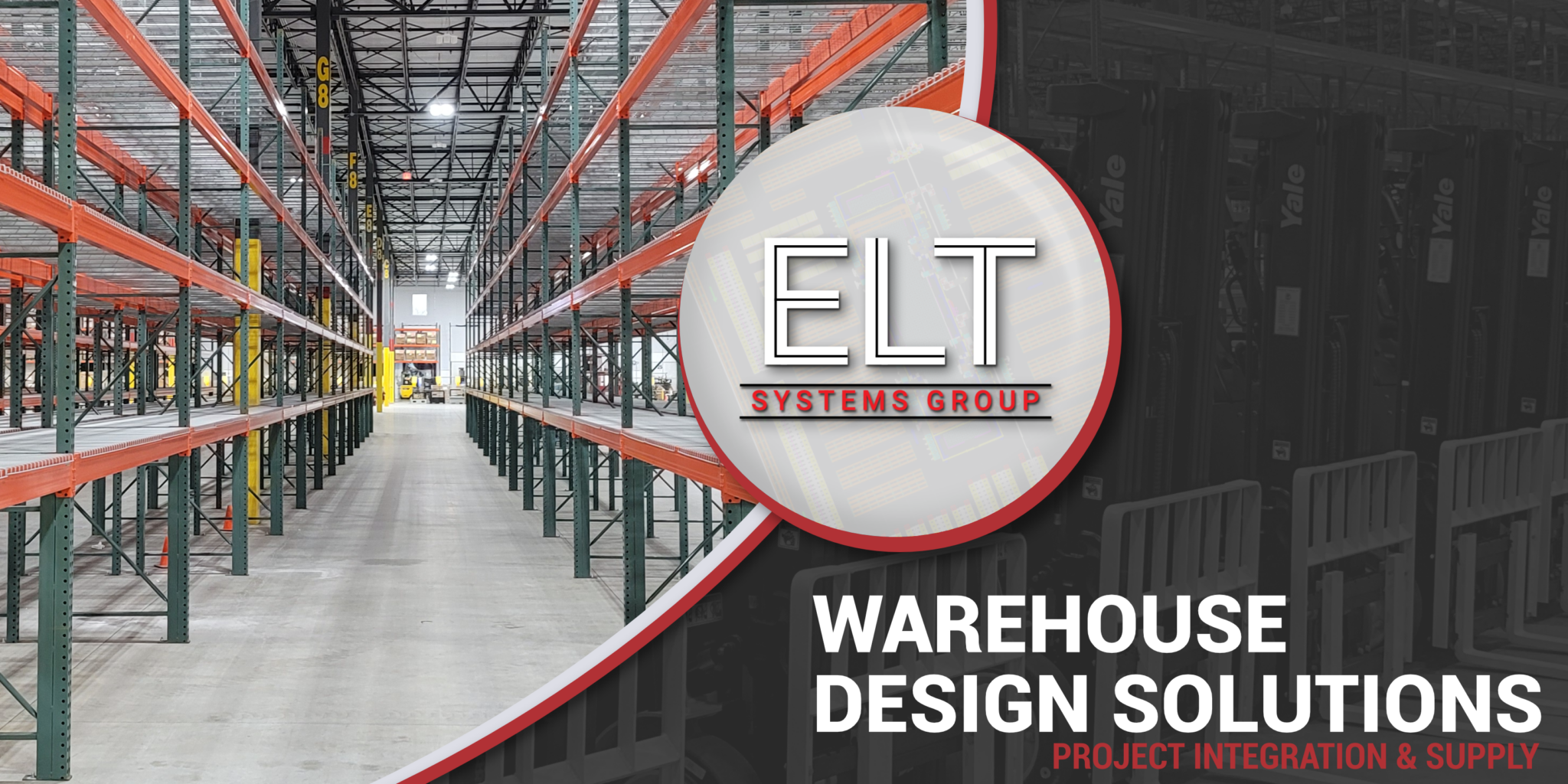
There are many operations that can benefit from utilizing Autonomous Mobile Robots (or AMRs). In this post we cover the Top Three Applications for AMRs in a warehouse space or manufacturing operations that help increase efficiency and throughput, while allowing your team to work smarter and not harder.
Number 1 – Dock to Stock
Modern workforce demands are complex, often requiring most, if not all tasks to be executed with precision and efficiency for the benefit of operations. Even so, “Dock to Stock” warehousing can be simplified into three overall steps: a) offloading pallets and materials from trucks; b) transporting materials within the warehouse facility; and c) putting product into storage/racking. One of the best uses of AMRs is to remove the tedious and repetitive nature of transporting pallets back and forth during long workdays. AMRs aid this process by moving the pallets or materials within the facility and allowing the human workforce to do the offloading and stocking processes—this is the most cost-effective way of implementing AMRs.
Number 2 – Moving Work-in-Progress Goods
Manufacturing operations often have runners or miles of conveyors that move products from one work cell to the next. Delays in product transfer, or any labor issues along the way, hamper production which results in revenue losses. Using AMRs that transport heavy or light-weight bins from cell to cell saves tremendous amounts of labor or investments in conveyance infrastructure systems. Allow ELT Systems Group to construct a cart-based system that allows you to transport work-in-progress goods or primary/secondary packaging materials across your facility.
Number 3 – Outbound Factory Integration: Pallet Wrappers
Many end-stage processes require a lot of steps to prepare for outbound shipments; for example: First, an operator needs to move pallets to a pallet wrapper, then they must engage with the wrapper. Then, the product must be staged for QC checks or sit and await shipping instructions. With the integration of AMRs, forklift operators can stage product near racking and call for AMRs to handle easier, time-consuming tasks. AMRs can take pallets to the dock area, automatically engage with a pallet wrapper, then stage the product accordingly at the dock doors. This allows for operators to continue with more complex tasks and contributes to a more efficient workforce.
There are many more applications that are both simple and complex in any facility, but these are some examples that occur in Phase I AMR deployment.
If you are interested in learning more about robotic solutions from ELT Systems Group, please contact us. Free consultation is available as well as the possibility of a robotic demo at your location.
Jason Dodge
Automation Manager | Systems Division
Eastern Lift Truck Co., Inc.
Cell: (609) 605-1043
Email: jdodge@easternlifttruck.com