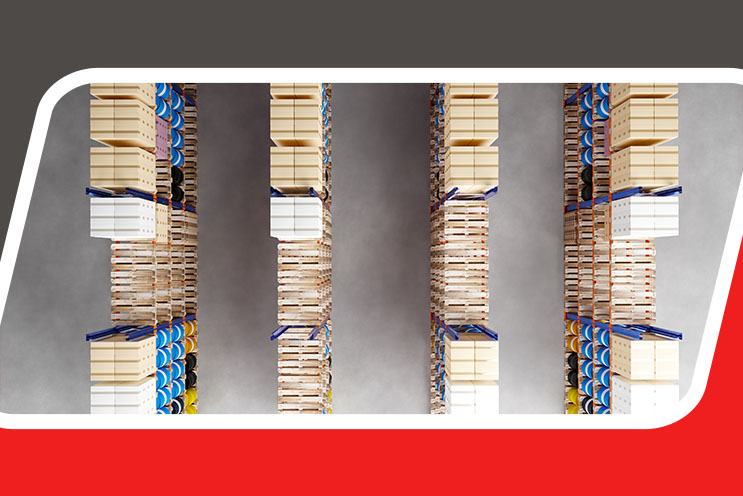
Warehouse layouts significantly impact operational efficiency. Proper layouts provide safer spaces for workers and allow seamless equipment options. Having an organized facility can also lead to boosted customer satisfaction and maximized revenue.
Creating a new warehouse layout can seem challenging, but the right tips can make the process easier and ensure you maximize your space and productivity.
Why Is Warehouse Layout So Important?
Your warehouse layout encompasses the facility space and dictates how equipment, workers and materials move throughout the warehouse. A warehouse’s unique building features, product types and equipment usage can impact design possibilities. For example, hazardous materials may require specialized, secure storage space.
The proper layout can boost overall efficiency by enhancing safety and empowering workers to move goods quickly through the space. Small changes like placing items workers frequently need in reachable areas can minimize strain and injuries while boosting productivity. Larger modifications, such as moving aisles to maximize space and using forklifts to carry goods, can also make a significant impact.
Along with creating a more efficient workspace, the right warehouse layout can help companies remain OSHA compliant, prepare for audits and make the most out of budgets. Additionally, a well-planned warehouse layout can help managers reduce unnecessary spending on equipment or goods and eliminate the need for additional buildings or space. Keeping the facility organized can also lower fire risks, prevent accidents and provide a framework for emergency procedures.
How to Choose the Right Equipment
Investing in warehouse equipment is a key part of improving your warehouse’s efficiency. Although you can choose from a vast selection of equipment, your space will likely dictate which pieces will make sense in the warehouse.
Many warehouses can maximize productivity by using equipment like forklifts or pallet jacks. A forklift can move goods indoors and outdoors and make quick work of transporting items around the facility. Pallet jacks transport small loads across short distances. These equipment pieces can enhance your operations, but there are various models and sizes you can select for maximum efficiency.
Warehouse space is expensive and maximizing storage capacity and efficiency is usually the number one point of discussion when we work on projects with our customers. Whenever possible, we attempt to “shrink aisles” and add more vertical storage space in the form of higher and tighter racking.
Start with this simple formula:
Basic Right-Angle Stacking Width + Load Length + 12 Inches = Minimum Forklift Aisle Width
The basic right-angle stacking width is the least amount of space a forklift requires to make a 90 degree turn and enter a pallet. This measurement may be found on the manufacturer’s product page, specifications brochure, or by contacting the Eastern Lift Truck Co. Sales team.
Of course, load lengths vary depending on the product and pallet type you handle. The most popular pallet is the GMA pallet, which is 48” long x 40” wide. For more on pallet types, you may want to read this blog post.
The 12 inch measurement in the formula is the generally accepted space needed for trained forklift operators to clear any obstacles, such as other pallets or rack uprights.
We created the above chart to provide some general guidelines on forklift aisle widths. As you will notice, aisles may range from as wide as 14 feet to as little as 3 feet.
Traditional sit-down, internal combustion engine (I.C.E.) forklifts require the most aisle space to operate – as much as 13 to 14 feet. Electric rider forklifts typically work in a 10.5- to 12-foot aisle and single reach trucks are designed to function in 9-foot aisles.
Navigating aisles less than 9 feet wide, requires smaller or specialty models of forklifts, assuming they are capable of handling your loads properly. Always consult the manufacturer’s guide for capacities and load centers.
Forklifts capable of navigating very narrow aisles are called VNA trucks, for short. For example, Aisle Master forklifts have an articulated mast, and will work in 6.5- to 7-foot wide aisles. Turret trucks from Hyster and Yale generally function in a 6-foot aisle. Sometimes VNA forklifts are placed on wire or rail guidance. By removing operator steering errors from the equation, these forklifts are able to travel through extremely tight aisles.
Operations that perform manual order picking may be able to only use order selector style forklifts and shrink their aisle to as narrow as just 3 feet.
Determining the correct aisle width for your warehouse requires a good deal of knowledge and planning. Before designing your warehouse space, consider both your current and future product handling. Will weights or dimensions change? Might you need to move some of your racking or shelving units to accommodate process flows within your facility? We already mentioned the right-angle stacking specification of the forklift. You will also need to account for the use of front-end attachments on your forklift, which extend the overall length of the trucks. Review your rack type and layout. Consider the average skillset of your forklift operators.
Our team is always available to help you determine which equipment will be the most beneficial for your facility before designing your space. We provide engineered drawings and professional guidance for racking layout and aisle width. Here’s an example of a drawing for a Combilift Straddle Carrier on rail guidance.
Warehouse Layout Ideas and Considerations
There are several key components to an efficient warehouse and unique factors businesses must consider when designing a layout:
- Receiving: In this area, workers unload incoming shipments, check the items and sort them. This area is often inside the facility with a bay connection for truck and vehicle access.
- Storage: Keep your inventory in the storage areas. This space should feature an accessible design and have connections to packing and receiving areas for efficiency.
- Packing: Employees pack orders in this location.
- Shipping: Team members can prepare outgoing orders in the shipping area. This location usually connects with the shipping bay and offers enough space for forklifts or pallet jacks to load completed orders onto distribution trucks.
- Service: Your team will need additional service areas like restrooms, break rooms and management offices to support their routine operations. Ensure you consider these areas during the design phase.
Despite the commonalities between warehouses, several factors make each business unique:
- Operation type: Your unique operations will impact the facility’s design. For example, a distribution center will likely have a different layout than a facility with a manufacturing operation. Manufacturing facilities may need more space for production, while a distribution center may need more storage space.
- Product type: Some goods and materials have special storage requirements. For example, businesses handling food may need cold storage spaces for perishables and dry storage sections for other goods. In comparison, a facility handling toys or clothing likely won’t need to make these distinctions.
- Safety: Safety should always be at the forefront of your operations. You must check with local policies and regulations and maintain compliance with regulated entities. These organizations and rules may dictate the number of exits in the facility, aisle clearances and more.
- Workflow: Your design will affect how people, goods and equipment can move throughout your facility. Consider your facility’s different areas or zones and create a design that allows for a seamless flow. If you’re adding packaging or manufacturing areas to the warehouse, it may be helpful to implement a tunnel rack system.
Steps for Designing a Warehouse Layout
Although each facility has individual needs, there are several best practices you can follow to design your warehouse layout:
- Outline the workflow: You can determine whether an I-shaped, L-shaped or U-shaped layout will work best by outlining your workflow. U-shaped facilities offer a straightforward flow, with receiving and shipping functions happening on opposite ends. I-shaped layouts are ideal for high order volumes and model an assembly line. L-shaped facilities have less back and forth to deter congestion, with storage at the angle of the L.
- Define workspaces: Creating a one-way workflow is typically the most efficient way to operate, but determining what essential workstations you need and your available space can help shape your design. You can also create pathways using arrows, signs or floor tape to minimize congestion.
- Optimize storage space: Consider which items your team frequently accesses, and place these items in easy-to-reach spots. Optimize racks and ensure it’s easy to move large amounts of inventory to different stations if needed.
- Obtain a WMS: Warehouse management systems can improve productivity and increase warehouse performance while reducing errors. These systems can impact your workstations and layout, streamlining some processes.
- Collect feedback: You can determine your layout’s success by asking your team how they feel about the change. Implement new ideas to streamline workflows and adjust stations as necessary. This feedback is an excellent way to identify pain points and opportunities for more efficient processes.
Design Your Warehouse Layout with Eastern Lift Truck Co.’s Warehouse Products Group.
Designing a new layout can be easy with the right partner. Whether you’re starting fresh or have a clear idea of what you’d like to accomplish, the consultants at Eastern Lift Truck Co. can help. Our consultants can design the optimal layout for your facility to maximize storage, productivity and efficiency.
Our team uses computer design software to create layouts, visualizing the best use of your space. We always account for your equipment, products and square footage to craft spaces incorporating storage systems, offices, work platforms and anything else you might need. Our comprehensive process includes conceptualization, project management, integration and maintenance, empowering us to help you from start to finish.
Learn more about our services or how we can help you by connecting with our team today.