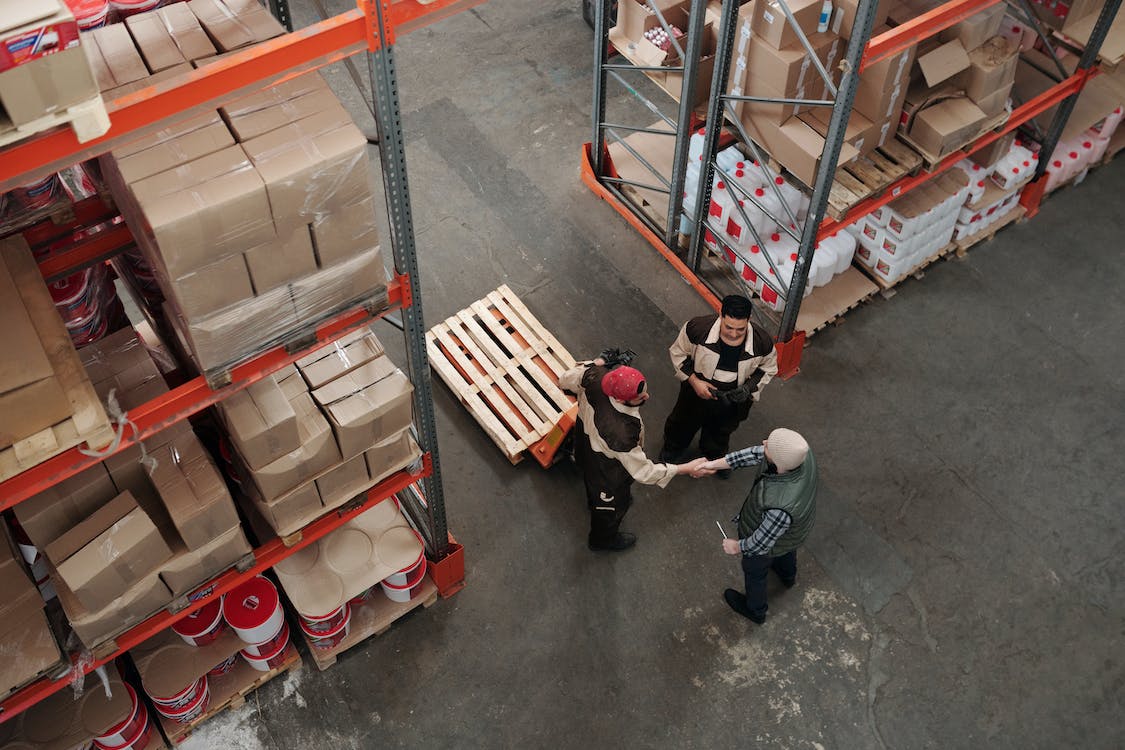
Within a manufacturing cell, pallets containing materials come in, and empty pallets need to be returned. These pallets can contain anything from packaging material, work in progress goods, or raw materials. Once the product is used up, and more is required, empty pallets need to be removed, or stored for future disposal.
Robotic lift trucks have the best return on investment when they are continuously working. A robot can be used to not only drop off full pallets but then be used to pick up and remove empty pallets. This can potentially free up time for operators to do other more important tasks.
Solutions: Intelligent Pallet Detection, Push Button Configuration
Trucks to Consider: Yale or Hyster Robotic Lift Truck or an OTTO Lifter
Intelligent Pallet Detection
One of the unique features is intelligent pallet detection. This feature allows a robot to scan staging lanes regardless of if the truck is engaged in a mission at the time or not. This allows the robot software to trigger pick missions and order other robots in the fleet to do work that is waiting for them.
This creates a fully autonomous solution that removes another the need for a manual operator to trigger picks and drops. This also requires no warehouse management system (WMS) / enterprise resource planning (ERP) integration allowing for fewer complex installations.
Push Button Configuration
In any installation, missions need to be triggered by some sort of event. Without WMS integration, sometimes those triggers include manual interface with the robot’s HMI or intelligent pallet detection. If those are not options, then ELT Systems Group can offer a manual button option where each button can be assigned a mission trigger. These triggers can be anything from signaling a robot to pick from a single position and drop at another or empty out staging areas or specific lanes.
Why automation provides an advantage.
As is the case with many industrial settings, including logistics, warehousing, and manufacturing, the labor pool has been shrinking. With finding labor an issue, robotic lift trucks offer a solution for any operation that requires simple repetitive movement that allow management to move existing labor to more skilled positions.
With the proper applications, a robotic material handling equipment can provide a fast Return on Investment by reducing an operations labor costs. There are other potential realizations of cost savings include: increased productivity from increased cycle efficiency and solving poor attendance as well as the damage reduction of products and equipment.
Why ELT Systems Group
Support Across North America
ELT Systems Group is part of Eastern Lift Truck Company that is staffed with hundreds of qualified service people. The Systems division is equipped with engineers along with their OEM partners to bring you 24/7 support and the ability to travel anywhere across North America to support your operation.
No Infrastructure
ELT Systems Group’s robotic solutions require no additional infrastructure to navigate in your facility. This means no reflectors, no magnets or wires in the ground. This technology allows the robots to navigate and drive within an existing facility without any other considerations outside of safety.
Dual Mode
The robotic Tugger and Lifter solution is a standard truck that has been built to be autonomous. This means that it can be used in manual mode as well as autonomous mode. Any operator (if the client allows for it) can take control of the robotic lift truck for any purpose.
Click this link to view our other application briefs.
Interested in learning about automation options for your specific application? Contact Jason Dodge today to get the conversation started.
Jason Dodge
Automation Manager | Systems Division
Eastern Lift Truck Co., Inc.
Cell: (609) 605-1043
Email: jdodge@easternlifttruck.com