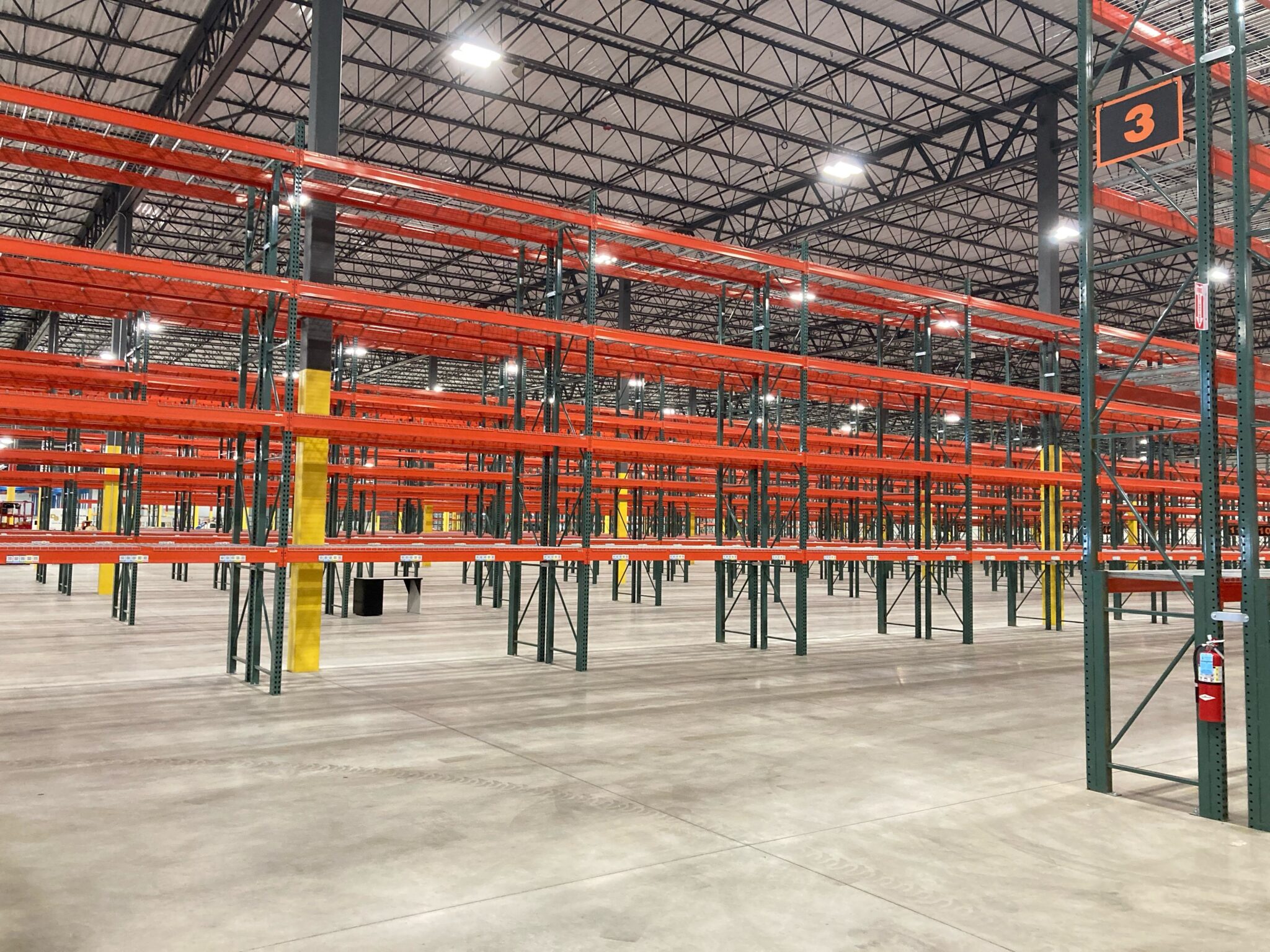
Shifting consumer habits and labor shortages are forcing many companies to change how they operate. As supply chains change, adapting to adjust to the new economy becomes a must. Some of these challenges include rearranging warehouse spaces to accommodate new workflows, utilizing newer material handling vehicles, and finding ways to increase the bottom-line capacity.
If you are navigating the task of rethinking your manufacturing spaces and facing new logistical challenges, here are a few things you may want to consider when planning your warehouse design. Keep in mind that ELT Systems Specialists can assist with direction and any concerns you may have.
Adding a Tunnel to a Rack System
Perhaps you have added new manufacturing or packaging areas to your operations, and you want to be able to bring material handling equipment directly to it, instead of taking more round-about routes. Sometimes you cannot take out beam levels without considering the initial design. Some uprights are designed with lower beam levels as a structural element. Make sure you have enough room for the turning radius of your equipment, as well as two-way traffic. Also take into consideration that by adding intersections, you may be creating additional traffic and exposing these uprights to potentially more vehicle strikes. However, adding in frame protectors or end of aisle guards will help to combat strike damage.
Get a Rack Inspection First
In most cases, if you are re-designing your warehouse space, you won’t be moving new racking. If you are moving existing racking, it is paramount to get an inspection of all materials before you move them. Without this preventative measure, unsafe situations could be created by reusing old racking materials. Reusing damaged rack can cause the new structure to fail. Damaged beams or uprights in a new design can come under different stresses that could cause them to fail faster than in their previous configurations. Recognize that damaged or deflected beams might cause failure if they are being used in different weight capacities.
Update the Design to Align with your Current or New Material Handling Equipment
You probably had completely different material handling equipment when you installed your old racking. When changing your layout, you may want to consider a few different specifications before completely duplicating it: Check to make sure your aisle widths are correct. You may have newer equipment that doesn’t require the same aisle width and saving space in the aisle may accommodate additional rack capacity. Make sure your top beam levels can be accessed by your equipment, especially if you are getting new equipment soon. Build the rack around your equipment.
There are many other factors to take into consideration. One aspect might be to look at newer fork truck designs than you currently use; for example, Very Narrow Aisle (VNA) forklifts allow you to minimize your aisle widths from 11 feet to 6 feet which can help you get the maximum storage capacity per square foot and increase your storage capacity up to 50% when compared to conventional aisle widths. New warehouse design layouts can create more pallet positions by burying building columns in the flue space rather than in a bay. Let out Specialists help you explore all the options you may not have considered. We can help make sure your move is optimized for your operation while ensuring your material flows smoothly.
Jason Dodge Automation Manager | Systems Division Eastern Lift Truck Co., Inc. Cell: (609) 605-1043 Email: jdodge@easternlifttruck.com