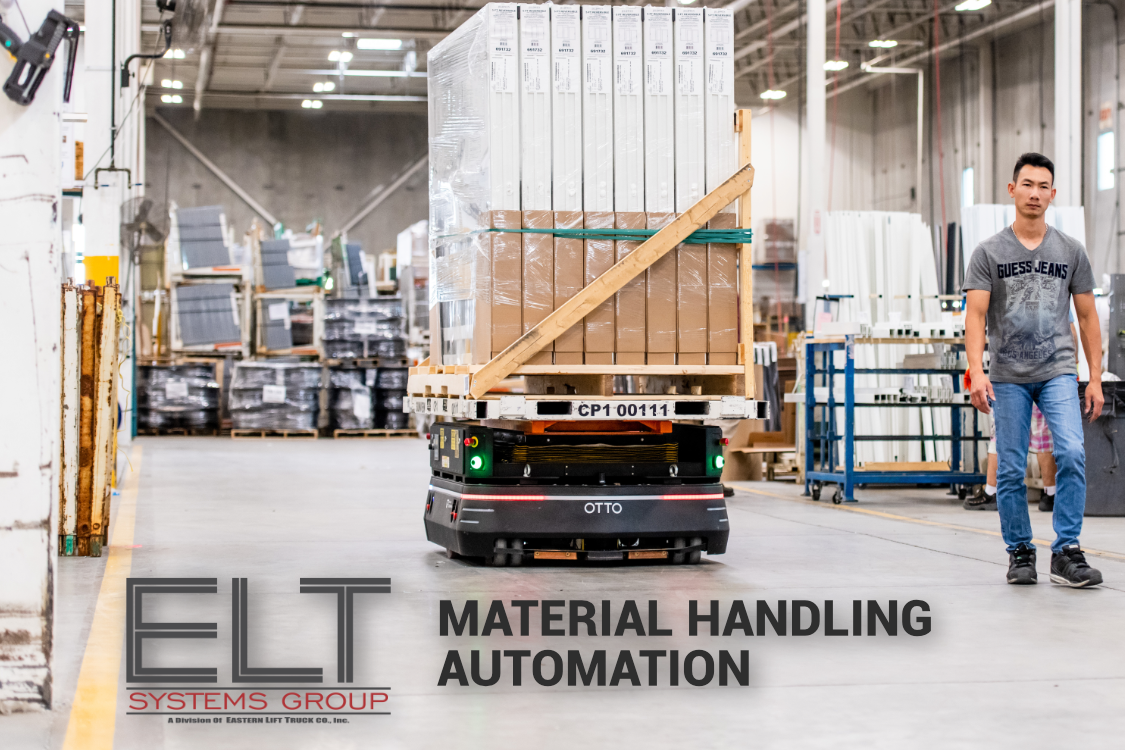
Autonomous material movement technologies, specifically autonomous mobile robots (AMRs), have gained popularity as the answer to labor shortages, supply chain disruption and employee safety concerns in manufacturing facilities around the world. As you research options, you will want to understand what technologies are available, how they differ, and the related costs, to implement them.
Every autonomous mobile robot (AMR) project budget has two main drivers beyond the cost of the hardware itself: factory integration and robotic deployment. Factory integration is different for every project. It can range from integrating AMRs with a stretch wrapper or a conveyor system, to fully integrating with a Warehouse Management System (WMS). All this is done with a variety of PLC brands, different equipment manufacturers and software developers.
Robotic deployment is the act of setting up the AMRs to navigate through a facility, conform to traffic rules, and pick up and drop off materials in a safe and measured way. Deploying AGVs or AMRs has normally been measured in weeks and months, but with highly sophisticated software and technology, AMR deployments are now being measured in days.
Join us at our webinar on August 16, 2023 to learn more about the costs associated with a robotic deployment and other factors to consider as you begin your research for autonomous material movement solutions.
What goes into the investment of a typical robotic deployment?
Your robotic deployment investment is influenced by four main factors:
- Project Management
- Time Spent Onsite
- Engineering Time
- Travel Expenses
Each of these factors share a common variable: time. The longer the deployment, the more costly the project is. Throughout our years of implementing highly complex automation solutions, we have found solutions that offer easy-to-use software, prompt service and comprehensive training do the best job of bringing down the cost of ownership by as much as half or more. One AMR vendor that consistently checks all of these boxes is OTTO Motors.
If you have investigated AMR technology in the past but found the ROI was not suitable, it may be time to contact us to start a new review. Let’s explore why.
The right AMR solution reduces your cost of ownership and improves ROI!
- An easy-to-use software platform will simplify deployment and minimize onsite time.
- Having detailed training resources will empower you and your team to be self-reliant in troubleshooting and making your own adjustments.
- Partnering with a local, fully trained service provider will help you deploy and maintain your AMRs quickly and efficiently, reducing downtime.
As you begin your AMR journey, one of the most important features to consider is the software that drives the solution. There is immense value in working with a flexible platform that is not overly complicated to learn and be able to train others in its operation.
What AMR software features can help minimize expenses?
- It does not require a computer programming or engineering degree to learn and operate.
- It is easy to modify the placement of pick and drop locations.
- It is simple to add new traffic rules such as stop signs, slowdown zones, and do not enter areas.
- All changes can be made quickly, allowing users to iterate and test.
Other forms of automation (specifically robotic palletizers, stretch wrappers, and packing equipment) operate comfortably within defined cells where their job is repeated to the specified inch all day every day. On the other hand, AMRs operate safely in an open space, around people and moving equipment, from one side of a facility to another.
What this comparison means for managers is that no installation or deployment is perfect from day one. Your operation will shift and adapt to the presence of AMRs in your facility. There are always tweaks and changes you would want to implement when unforeseen circumstances arise in your live environment. AMRs can provide you with that flexibility. For example, if you notice certain areas may cause delays for your AMR, you can change its route or add an intersection where it stops.
With other technology, these changes would typically require a specialist or engineer to visit your facility to program these changes into your system and test them. As you can imagine, this would typically be a costly visit. AMR technology often doesn’t require this investment. For example, OTTO Fleet Manager enables these simple changes to be made easily with proper training by an OTTO Motors material handling expert. No programming or engineering knowledge is needed.
To learn more about the differing technologies and whether autonomous material movement is the right solution for your facility, reach out to the experts at ELT Systems Group today and then join us on:
Wed. August 16, 2023 for Ask An Expert: How To Start Your Autonomous Material Movement Journey.